“降本增效”一直是光伏制造的最大的主题。作为光伏系统最核心也是成本占比最大的部分——光伏组件,就成为了光伏制造的核心战场。
光伏工业化发展这几十年来,通过光伏人的不懈努力,光伏系统成本下降飞速,效率提升明显。特别是中国光伏制造崛起的十余年来,无论光伏系统成本,还是组件价格都下降到之前的1/10以下,系统发电效率也提升了近一倍。取得辉煌成绩的同时,光伏人也发现,近年来“降本增效”愈发困难,每一小步的进步都越发艰难。面对来自市场和竞争的压力,制造企业们纷纷绞尽脑汁想尽办法,去降低成本。
要说“降本增效”目前最热门的关键词——“大尺寸”一定包含其中。无论各大展会,还是网络、论坛,大尺寸硅片、大尺寸组件都频繁出现在人们视野中:硅片从过去常规的156mm,提升到更大尺寸,如:隆基主打的M6硅片(166mm),中环新推出的G2硅片(210mm)。
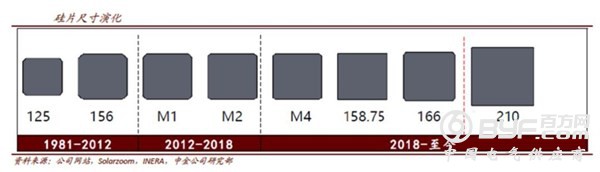
组件也从常规的60、72片规格,近期推出78片规格、甚至96片规格大组件。借助于大尺寸组件,2019年中国光伏仿佛进入了大跃进时期,组件从3.0(300W+)时代,一跃进入了4.0(400W+)、4.5(450W+)、5.0(500W+)时代,甚至有企业宣称达到6.0(600W+)时代。
大尺寸是否真能成为光伏追求“降本增效”有力法宝呢?
一、 “大尺寸”的价值分析
我们先来分析下大尺寸硅片的价值:
首先要说明的一点大尺寸实际对于电池效率(单位面积发电量)提升并没有帮助,仅仅是通过增加面积提升电池片的功率。
对于硅片制造企业而言:
1, 大尺寸硅片(单晶)可以降低硅片的每瓦能耗成本。通过对单晶拉棒直径的适当增加,进而做出相对大的硅片,可以降低硅片的单瓦成本。
2, 大尺寸硅片可以降低切片成本。大尺寸硅片,相同瓦数的硅片数量减少,相应的切片成本可以降低。
单晶硅片企业成本三大组成:硅料、拉晶、切片。大尺寸硅片的启用可有效的降低其中拉晶、切片能源和耗材成本。
对于光伏下游制造企业而言:
1, 大尺寸硅片可以提高从硅片到组件的生产效率。简单说,反正都是切一刀,翻一面,涂一遍,压一次…… 片子大点电池生产效率(按瓦数计算)就会得到提升。
2, 大尺寸硅片可以降低生产运营成本。硅片大了,相应单瓦的加工成本降低,人力、水电成本,设备折旧等都可以降低。
对于电站客户而言:
1, 电池倒角变小或取消,将会增加组件的实际发电面积,会有较小的增益。
2, 对于客户而言,单纯的电池尺寸变化,如果组件尺寸没有变化,实际发电效率并没有变化,并不能起到“降本增效”的作用。
我们再来分析下大尺寸组件的价值:
对于组件制造企业:
1, 大尺寸组件可以提高组件的生产效率、降低加工成本、运输成本等。
对于客户而言:
1, 大尺寸组件可以减少电站与组件数量有关的建设成本(比如:支架,电缆,基础压块,运输安装费用等)。
“大尺寸”价值总结:
1, 大尺寸硅片的价值(收益):硅片制造企业>下游制造企业>电站客户。
2, 大尺寸组件对于组件制造企业降本价值还是比较大的。
3, 大尺寸硅片对于电站客户而言(如果组件尺寸不变)实际价值不大,但大尺寸组件对于电站客户降低成本是有一定的帮助的。
二、 尺寸越大越好吗?
上面的结论是否完全正确?硅片、组件尺寸越大越好?
实际上,大尺寸硅片和组件并不是越大越好好。尺寸在增大的同时也会带来一定的副作用和隐患。
对于制造企业:
1, 大尺寸硅片,如果不是新建线,原有设备工艺是否能够匹配?如果要改造,改造费用多少?加上改造费用后,是否能够实现降本,就需要具体计算了。
2, 大尺寸硅片,可能会增加工艺的不稳定性,比如:可能增加碎片率,可能降低硅片的减薄适应能力等。
3, 大尺寸组件,会降低组件的力学稳定性和抗压能力,要维持组件能力,就要增加组件相关部件的厚度或强度,会增加一定成本。大尺寸带来的成本节省,是否超过由于尺寸变大,对于组件强化带来的成本增加?同样需要具体计算和分析。
对于电站客户:
1, 大尺寸组件增加单块组件功率的同时,也增加它的自重,以及面积,对于支架强度的要求,也相应提高,相应也会增加支架的成本。基础、运输费用也相应如此。
2, 大尺寸组件增加了安装人员安装难度,有可能会增加安装人员数量或时间,相应增加安装成本。
3, 大尺寸组件增加单组件功率,电流变高,会增加系统内部功率损耗。
总结:“大尺寸”并不一定就会带来成本下降,需要具体问题具体分析。
三、 “精益制造”思路下的“大尺寸”思考
在目前追求成本极限的大趋势下,“精益制造”重点之一就是“刚刚好”,产品在符合相关产品质量(安全)标准、满足客户需求的基础上做到“刚刚好”,不留半点多余浪费(冗余)。
在这样的思路下,“大尺寸”产品,大一点点都势必要增加产品的强化和安全成本。举例:我们原来用于支撑60片规格组件的支架系统,如果换成72片组件就必须要增加原有支架系统的强度。如果有人告诉你原有支架系统同样可以支持72片组件,那就说明原有支架系统,浪费了一定冗余强度成本。大尺寸组件对于边框、玻璃等同样如此。
所以,光伏降本追求极致的背景下,要求我们针对不同尺寸和使用环境的进行精密的计算,进行匹配性的设计与制造,从而追求极致成本。另外,我们也不能把利用(甚至透支)原有的冗余强度,理所当然的当作成本节省降低。
四、 “大尺寸”不是光伏“降本增效”的最佳法宝
“大尺寸”对于光伏的“降本增效”效果有限,并且还有一定条件限制,制造企业要根据现有设备工艺情况决定最合适的电池片和组件尺寸,对于电站客户而言要根据现场条件决定最佳的组件尺寸。
工业制造最重要的就是标准化,客户实际上也很难有能力去计算判断哪个尺寸是最合适自己的,所以希望协会、研究单位能与企业一同分析计算出一个各种环境条件下的最佳尺寸出来,并进行推广,省去市场的重复试错,造成不必要的浪费。
所以,“大尺寸”不是光伏“降本增效”的最佳法宝。组件的“降本增效”还是要更多的回归到组件高效技术本身。比如:爱康目前主推的高效电池异质结、双面、叠瓦等技术就是很好的组件“降本增效”方向。高效电池才能从本质上提升光伏组件的发电效率,目前异质结电池实验室效率已经达到26.63%,量产也达到24%以上。双面组件,相对单面组件可以提升组件10-20%实际发电量,匹配跟踪系统效果更好。叠瓦可以降低组件热斑风险,提升组件有效发电面积,减少组件电流、降低工作温度,从而提升实际发电量。